Low ash Binchotan. Excellent Fire Strength and Longevity.
Mr. Tanaka’s charcoal-making hut is located 30 minutes drive from the Gobo Interchange. Rising up at the back of the hut, the kiln has a powerful presence.
Binchotan is characterized by its crystallized carbon, making a high metallic sound when struck. It is very different from standard barbecue ‘black charcoal’ in terms of its much greater burning power. Mr. Tanaka burns binchotan charcoal to keep warm in the hut; the whole charcoal glows red and radiates heat like neon lights; it has such captivating beauty.
「 Binchotan is hard to light, but it has a high firepower and a long life, so it doesn’t go out easily. Ordinary black charcoal is soft, so it doesn’t work like that. When I asked about it at yakitori restaurants and other businesses that use our binchotan, they said that once a fire starts, it lasts for a long time, so it’s cheaper.」
In addition to its good fire retention, another advantage of binchotan is that it produces little ash. The reason for the production of such fine hard charcoal can be found in the raw material, the ubame oak. The wood fibers are so dense and hard that it is not suitable as a building material, but it is the best material for making charcoal.
「I tend to use trees that are about 25 years old. I go into the mountains and do the felling myself with a chainsaw. And trees are naturally bent, aren’t they? I cut into them and straighten them out with komi [wooden wedges]. Otherwise they won’t pack well into the kiln. In other regions, the wood is put in the kiln lying down, but in Kishu it is stacked upright. The wood is then packed upside down with the base of the tree at the top. This allows the wood to drain off the moisture. The old people were clever, weren’t they?」
Each burning contains around 500 sections of wood, totalling 4 tonnes. The kiln is packed by hand, carrying wood through a small entrance barely large enough for one person to pass. This must be done while there is still heat from the previous charcoal burning. It is hard labor, fighting against the weight of the wood and the smoldering heat.
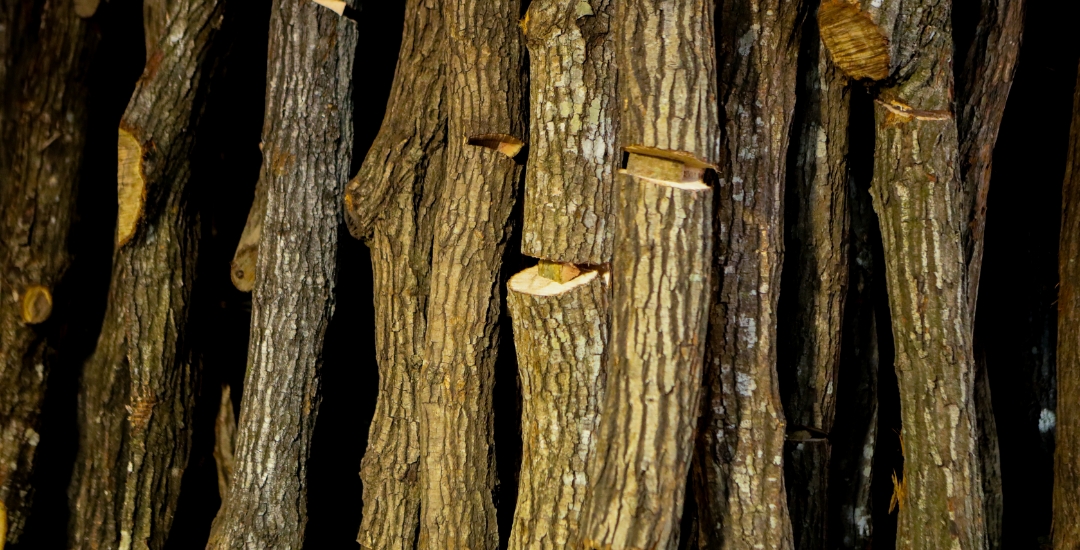
Straightening wood by cutting-in along curved sections of wood and inserting wedges.
Self-built Kilns. The Art of Fire Manipulation and Perfect Timing.
Each Binchotan maker builds their own kiln; piling up stones, coating them with local red clay, even building the domed ceiling by themselves.
「To become a fully-fledged charcoal maker, you have to be able to build a kiln. You learn by helping others, and through that experience you gradually learn to choose strong clay and stones that are suitable for the kiln. It took me 20 years before I could do it all myself.」
After filling the kiln with Ubame oak, the first step is to make a fire at the mouth of the kiln. The fire is lit through a 30 cm square opening at the foot of the entrance. The temperature inside the kiln is slowly raised. After three to four days of steaming, the wood’s moisture evaporates and it becomes dry, ready for the next stage of carbonisation.
「When the smoke changes color and starts to smell burnt, that’s a sign that carbonization has started. We block up the entrance and then burn it for another three or four days.」
Blocking the entrance means that the inside of the kiln is free of oxygen. This ensures that the wood does not reach its flash-point and combust, and is instead transformed into charcoal.
「When the charcoal is fully carbonized, it becomes black charcoal like incense sticks, so we open the kiln, little by little, and let the air in slowly to turn the charcoal a glowing deep red. This is called ‘nerashi’, or ‘arashi’. About once every 30 minutes, the opening of the kiln is gradually widened. We do this over a period of 24 hours, staying with the kiln overnight.」
When soft black charcoal, used for barbecues, is fully carbonized it is left to cool in the kiln. Binchotan, on the other hand, undergoes an additional burning process after carbonization called ‘nerashi’, where temperatures reach up to 1200°C. Nerashi produces a hard charcoal that makes a metallic sound when struck; unique to binchotan.
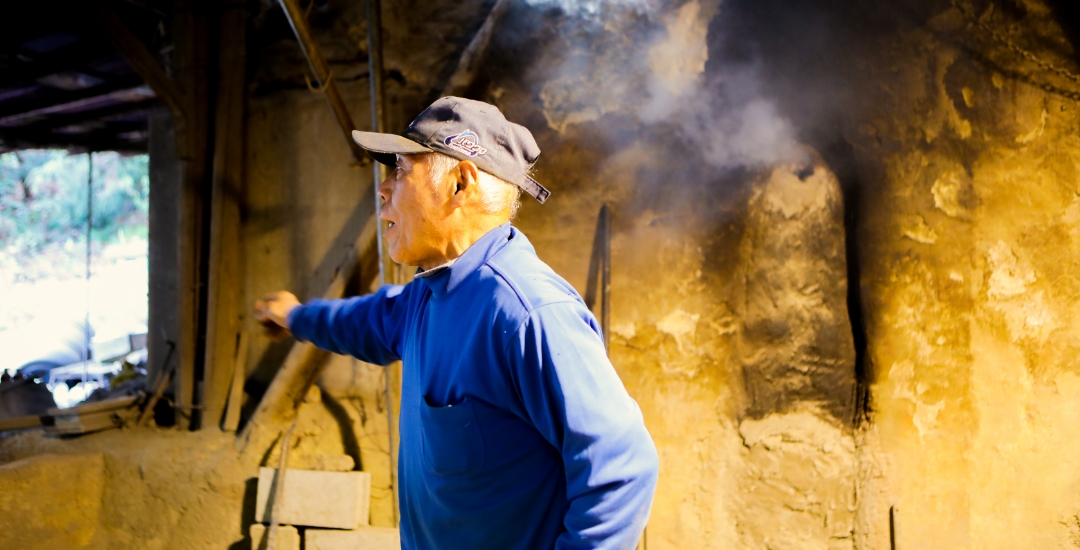
Charcoal Making: A tradition that continues to be passed down from generation to generation.
When the burning is finished, charcoal is pulled out of the kiln using an ‘eburi’, a long iron rake, and buried under ‘subai’, ashes from previous firings, where it is left to cool. This takes eight hours with only occasional breaks. Mr. Tanaka’s muscular upper body is testament to this hard work.
「The most enjoyable part is the moment when you take it out of the kiln. No matter how many times you do it, it’s always different, so you look at it and wonder what kind of charcoal you’ve made.」
Recently, some aspiring charcoal makers have migrated to Hidakagawa-cho from the city, and Mr. Tanaka has trained five or six people so far. The name Binchotan is said to derive from Binchoya Chozaemon, a charcoal wholesaler in the Kishu domain during the Genroku era (1688-1704), Edo period; credited with making the name ‘Kishu-binchotan’ famous. When you think about it, Binchotan has been known as the king of Japanese charcoal for almost 300 years.
The more we learn about binchotan, the more profound it becomes, and we cannot help but admire the wisdom of the ancients. We will continue to cherish it as an indispensable part of the「Narumi-ya Premium」range.
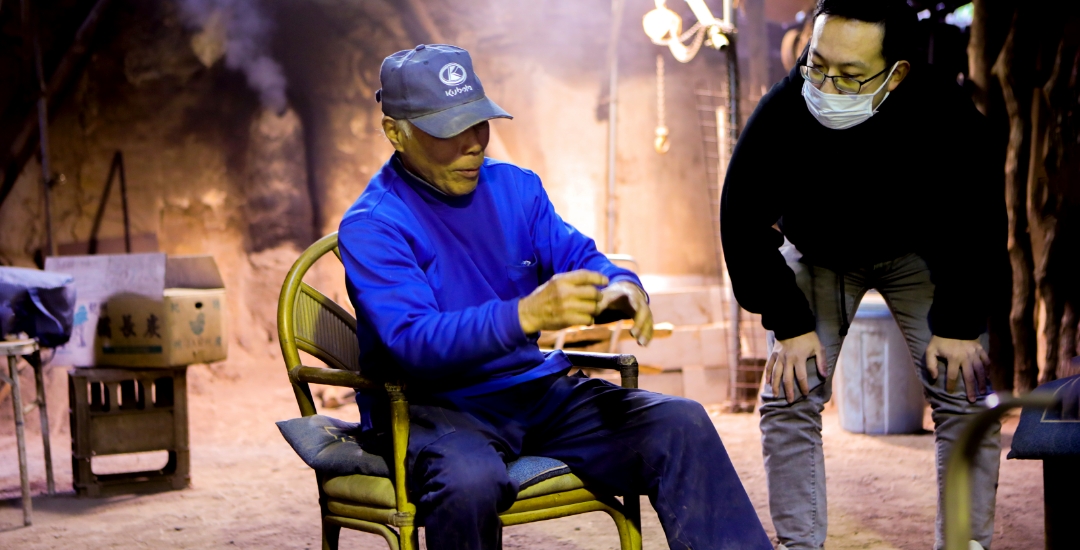